Water and electricity – without emissions
Wevo sealants and adhesives for industrial fuel cell manufacturing
Hydrogen-based fuel cells play an important role when it comes to decarbonisation in the transport sector. However, they are technically very complex to manufacture – and often still require a number of manual steps. Wevo materials ensure a very tight seal, opening up new opportunities for serial production, as confirmed in studies by ZBT, the Duisburg hydrogen and fuel cell centre.
Green hydrogen produced from renewable energy sources enables fuel cell vehicles to be operated without any emissions. However, enormous investments will be necessary before it is fit for widespread use; a study by McKinsey & Company cites a figure of around 320 billion dollars worldwide by 2030. It was also established that global electrolysis capacity for the production of green hydrogen will probably increase about 400-fold from 0.55 gigawatts at present to approximately 232 gigawatts.
Amongst other things, this green hydrogen is intended for use in the industry, buildings and mobility sectors. In the transport sector, the focus until a few years ago was on developing hydrogen infrastructure for fuel cell cars. It was reported in an H2stations.org press release that at the end of 2022, 814 hydrogen refuelling stations were in operation worldwide. According to information from the International Energy Agency, this contrasted with around 72,000 fuel cell cars. Yet out of all major car manufacturers, only Toyota and Hyundai are currently mass-manufacturing fuel cell cars.
Great opportunities in heavy goods traffic
Fuel cells are regarded as having especially great potential as a drive technology for transporting heavy loads – i. e. for commercial vehicles, buses, ships, in rail transport and in the long term also aviation.
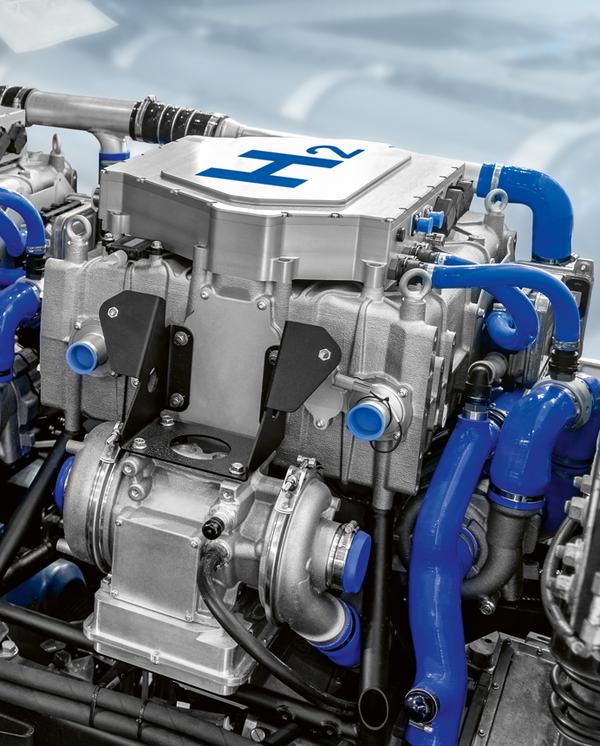
Fuel cells are regarded as having great potential as a drive technology for transporting heavy loads like trucks over long distances
Manufacturers from Japan and Korea have a knowledge advantage as first movers in the passenger car sector and are consequently leading the way. The South Korean capital of Seoul has ordered 1,300 fuel cell buses from Hyundai and has plans to take the bulk of its diesel-powered buses out of service. Toyota hopes to sell 200,000 fuel cell vehicles in 2030, most of them in the truck segment.
Fuel cell drives are also making an impact outside Asia. In Germany, for example, Daimler has been testing their Mercedes-Benz GenH2 truck since summer 2023 and are targeting a completely CO2-neutral fleet by 2039. Bosch, one of the world’s largest automotive suppliers, has announced that it will invest 2.5 billion euros in hydrogen and fuel cell technologies over a three-year period. Around two thirds of this will be spent on drive technology. The production of fuel cell systems for commercial vehicles has already got under way parallel to this in Germany and China.
Material requirements
Fuel cell systems are technically very complex and place high demands on the materials used. As the smallest of all molecules, hydrogen diffuses easily through most materials – and is also flammable. In oxygen-containing atmosphere, it can form an explosive gas mixture known as oxyhydrogen. Tightly sealed components – socalled bipolar plates (BPP), for instance – are therefore of elementary importance for the safety of fuel cells.
Challenges for serial production
Together with the membrane electrode assembly (MEA), BPPs are central elements of any proton exchange membrane (PEM) fuel cell (see graphic below). They ensure a steady supply of hydrogen and oxygen or air to the MEA while simultaneously controlling the release of thermal and electrical energy as well as the water which is produced.
To prevent hydrogen diffusion, sealing materials must not only have high gas impermeability; they must also withstand the challenging ambient conditions inside the fuel cell stack including humidity, temperatures up to 120 degrees Celsius or possibly low pH. Furthermore, if the bipolar plates have tolerances due to manufacturing, this results in uneven pressure distribution on the sealing materials, which has to be compensated while the stacks are being pressed.
Some manufacturers currently use prefabricated gaskets that are manually applied on both sides of each bipolar plate for sealing BPPs and MEAs. However, this approach is not suitable for automated production of high volumes.
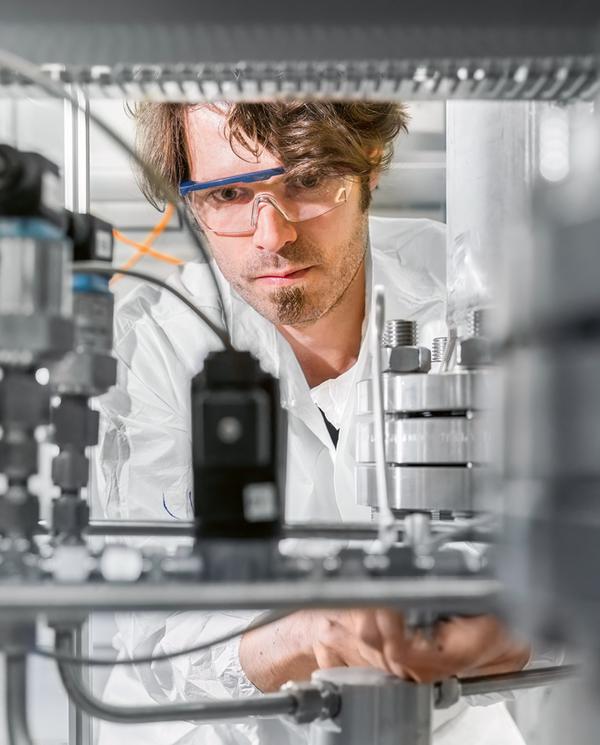
Experimental set-up for hydrogen technology at ZBT, the Duisburg hydrogen and fuel cell centre
In addition, there is a risk that the gaskets could become detached from the bipolar plate during stacking, so that they no longer seal effectively. Addition-curing silicone liquid gaskets, also referred to as cured-in-place gaskets, are used as an alternative in fuel cell production. Unfortunately, these have relatively high gas permeability and do not adhere well to the substrates.
It was against this background that Wevo developed special, chemically resistant two-component materials based on polyurethane and silicone for use in PEM fuel cells. They are applied as reactive liquid gaskets and have advantages for serial production and operation of fuel cell components provided the raw materials are carefully chosen. The hydrogen permeability of these materials has been tested using a special method by ZBT in Duisburg, one of the leading research institutes in the field of hydrogen and fuel cell technologies.
Low permeation coefficients confirmed by ZBT
The study showed a very low hydrogen permeation coefficient of about 130 E-8 cm²/s for one of Wevo’s silicone-based products after a 16-hour measurement period. This compares with values generally between 500 and 1,000 E-8 cm²/s for conventional addition-curing silicones.
Wevo’s polyurethane sealants, which have similar thermo-mechanical properties, have even lower hydrogen permeability. Depending on the Shore hardness setting, a permeation coefficient of between 30 and 70 E-8 cm²/s was determined following a measurement lasting 16 hours.
Better adhesion
Moreover, Wevo has optimised the adhesion of the silicone materials to take account of the most commonly used bipolar plate materials, such as stainless steel or graphite thermoplastic compounds, and reduced the compression set. Polyurethane sealants adhere to the different substrates even better. The significantly faster curing compared to silicones is a further argument in favour of polyurethanes when automating serial production of high volumes.
Adhesives for BOP components
Due to their good adhesion properties, polyurethane-based products made by Wevo can additionally be used as adhesives for other applications – both within the fuel cell stack and in the components and auxiliary systems of the fuel cell system, the so-called balance of plant (BOP). For example, it is possible to simultaneously join and seal the two half-shells of the bipolar plates using customised, polyurethane adhesives. Where metal BPPs are concerned, this joining method can be employed as an alternative to laser welding. With BPPs based on graphite/polymer compounds, durable bonding is a must.
The humidifier, too, is a crucial BOP component. It protects the sensitive polymer membrane of a PEM fuel cell from drying out. The humidifier components can be securely joined and sealed thanks to Wevo’s polyurethanes ranging from elastic and customisable for specific applications (e. g. WEVOPUR 79954/15) to tough (e. g. WEVOPUR 79086 T).
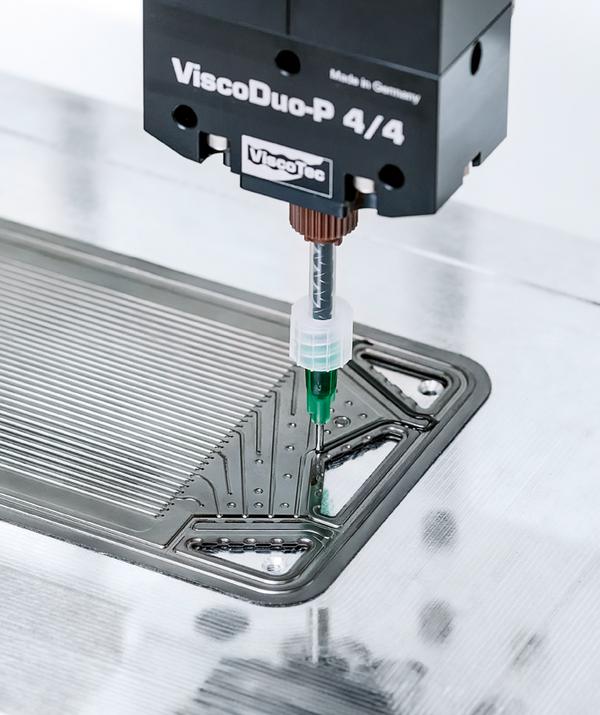
A silicone-based sealant (WEVOSIL 28002 A/B) is applied to a bipolar plate using a dosing system from ViscoTec GmbH
Apart from excellent adhesion, these adhesives are characterised by high ionic purity and low levels of volatile organic compounds (VOCs), which could otherwise damage the sensitive membrane and lead to a drop in performance. The special formulation also guarantees the necessary high hydrolysis resistance at temperatures of up to 100 degrees Celsius.
The anode recirculation blower or the air compressor installed in the air circuit are other applications in the BOP. In the latter case, Wevo’s epoxy resins and silicones enable potting of the stator for the drive motor. By optimising the thermal conductivity and crack resistance of the materials, the forces produced during rotation are compensated and any heat generated is removed in a targeted way. Special, thermally conductive, polyurethane potting compounds and silicone gels for the power modules are likewise used for power electronic components such as DC/DC converters, on-board chargers and control units.
Wevo products for use in electrolysers
Wevo has more special products in its portfolio for hydrogen production plants. The ZBT study confirmed a hydrogen permeation coefficient of only 3 to 4 E-8 cm²/s for Wevo’s tough polyurethane adhesives. The material is therefore suitable for bonding large stacks for PEM electrolysis plants, amongst other things.
Alkaline electrolysis plants require adhesive systems with even higher chemical resistance than is afforded by polymer membrane technology. The electrolyte they work with – an aqueous potassium hydroxide solution at 85 to 90 degrees Celsius – is responsible here. The majority of organic adhesive and sealing systems are not able to withstand such conditions permanently. Wevo has developed a specially optimised, highly cross-linked and chemical-resistant epoxy resin for this purpose.
New solutions for fuel cells and electrolysers and their components will also be in demand in the future. Wevo collaborates closely with research institutes and industrial partners in the search for the perfect product. The goal: practical solutions to meet the requirements of today’s – and tomorrow’s – technologies.
Order your Wevo magazine here
This article is part of issue #02 of Wevo’s magazine SCIO. Would you like to have a printed copy? Then you’re welcome to request a copy free of charge*.
Order form
* Only available to officially registered companies from relevant industries. We accept no obligation to provide a copy. Requests will be responded to by Email.
Image sources: Image 1: stock.adobe.com: Kari_designer, Image 2: scharfsinn86, Image 3: www.eventfotograf.in / JRF e.V., Image 4: ViscoTec Pumpen- u. Dosiertechnik GmbH
Links related to this article
Disclaimer (Extract) – Copyright and IP Rights: The contents published on this website are subject to German copyright and ancillary copyright law. Any utilization not permitted by German copyright and ancillary copyright law requires the prior written permission by the provider or the respective owner. This applies in particular to the copying, working, translation, storage, processing and reproduction of contents in databases and other electronic media and systems. Third-party contents and rights are identified as such in this regard. The unauthorised duplication and forwarding of individual contents or complete pages is not permitted and may possibly be punishable as a criminal offence. Only the creation of copies and downloads for personal and private and non-commercial use is permitted. The use of this website as external link shall only be permitted upon prior written approval oft he provider. Each and any firm or trademark is sole property of the relevant company. Citations of trademarks and names of third parties have a purely informative character. You will find the complete disclaimer in the imprint.